Graphite electrodes are one of the most versatile materials used in many different industries. In this blog post, we will look at three of the most common applications of graphite electrodes in a variety of industries.
From their use in the steel industry to their use in the automobile industry, we will explore the benefits of using them and how they can be applied in different industries.
By the end of this post, you should have a good understanding of the various applications of graphite electrodes and how they can be used to your advantage.
Introduction To Graphite Electrodes
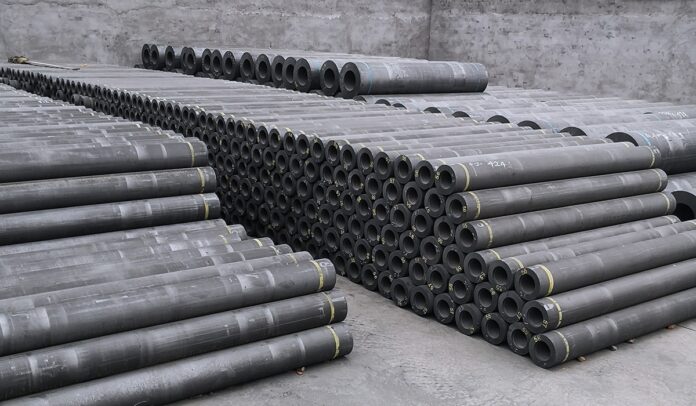
Steel is one of the most important materials in the world, and it’s essential for everything from cars to airplanes. However, the industry is always looking for new ways to make steel faster, stronger, and more durable. One way that steel manufacturers are trying to improve production is by using graphite electrodes.
They are special pieces of metal that are used in the smelting process. They’re specifically designed to help reduce the amount of heat that’s needed to turn iron ore into steel. This means that they can be used in a variety of different industries – from aluminum production to chemical manufacturing.
There are a number of advantages that using graphite electrodes have over traditional methods.
For example, they’re much faster than other types of electrodes when it comes to producing steel. This means that companies can save money on their overall production costs by switching to graphite electrodes.
Additionally, they’re less likely to cause environmental damage because they use less energy overall.
Understanding The Properties Of Graphite Electrodes And Their Applications
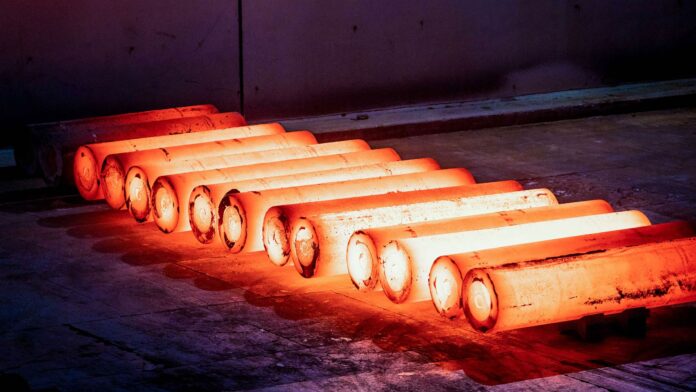
Understanding the properties of graphite electrodes and their applications is essential for anyone working with electrical components.
Graphite is a unique material that offers several advantages over other electrode materials, such as stainless steel and copper. In this section, we will take a closer look at the properties of graphite electrodes and their uses in the electrical industry.
- One important property of graphite electrodes is that they are very resistant to corrosion. This means that they can be used in areas where other metals would not be able to survive, such as high-temperature steel alloys.
- Additionally, they offer good electrical conductivity, so they can be used in devices that need to transmit large amounts of electricity quickly.
- They are also versatile and can be used for a variety of different applications in the electrical component industry. For example, they can be used in insulation materials for power cables or electric vehicles.
- They can also be used to make high-temperature steel alloys that are stronger and more durable than traditional steels. In fact, some aircraft engines are made using graphite electrodes!
- Another advantage of using graphite electrodes compared to other electrode materials is their lifetime expectancy. They tend to last longer than stainless steel or copper plates without deteriorating significantly over time.
This makes them an ideal choice for devices that require long-term performance and durability – such as industrial electrochemical machining processes or electric vehicles charging stations.
Graphite Electrodes In Steel Industry
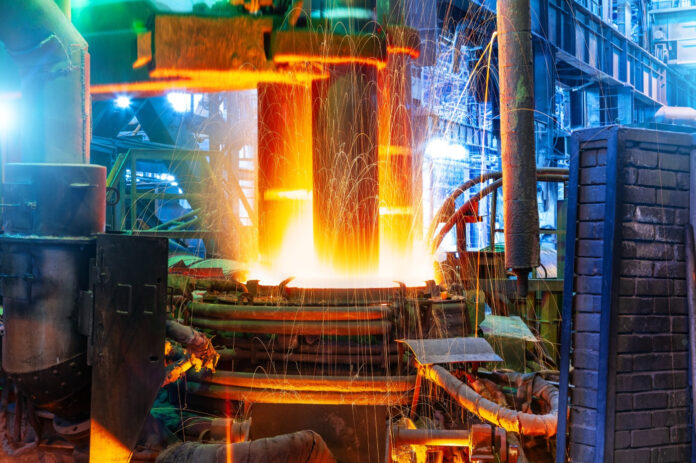
Steel is one of the most heavily used metals in the world, and it’s no wonder why. Steel is strong, durable, and versatile, making it a valuable asset for businesses and people alike. One important component of steel production is graphite electrodes. They play a vital role in the electric arc furnace (EAF) used for melting steel ore.
- The heat from the graphite electrodes allows for continuous melting operations – this means that you can make more steel faster without having to stop every few minutes to adjust the heat levels.
- Additionally, because graphite electrodes are known to be very cost effective and durable, they’re an ideal choice for high-volume manufacturing processes like the steel industry.
- They are also known to be environmentally friendly – they don’t produce emissions like other types of electric arc furnaces do.
- And last but not least, they are also known to be very easy to adjust – this is especially helpful when you need to make quick adjustments during high-power operations.
In short, graphite electrodes are an essential part of the steel manufacturing process and have many benefits that make them a great option for businesses of all sizes.
Graphite Electrodes In Glass Manufacturing
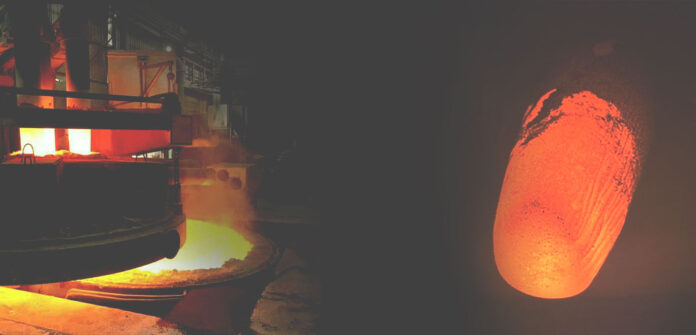
In glass manufacturing, graphite electrodes are used to produce molten glass from raw materials.
- Molten glass can be shaped and formed into large sheets or objects like bottles, vases, and lenses, among others.
- Additionally, graphite electrodes are designed to deliver precisely controlled thermal energy to both sides of the glass and give it a uniform shape. This means that the finished product will have a consistent look and feel regardless of where it is placed on the object.
- They are highly durable and can be used many times in the same glass manufacturing process without experiencing any problems.
Graphite Electrodes In Automobile Industry
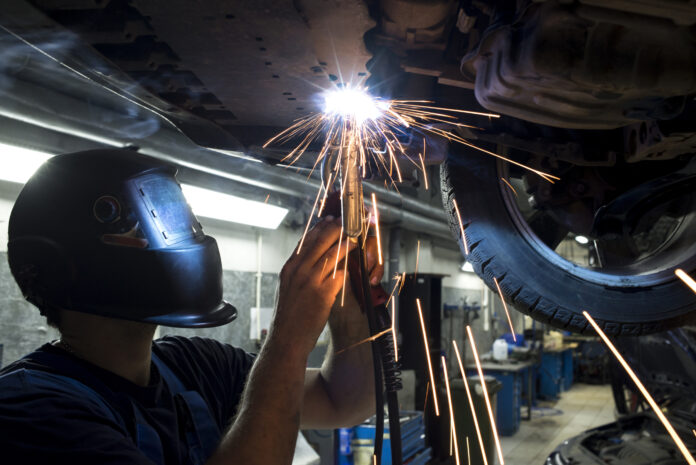
In the automotive industry, graphite electrodes are being used more and more to weld various parts together.
- They have a low contact resistance and provide excellent welding results. They are suitable for multiple types of welding, including spot welding and seam welding.
- They are also lightweight, durable and relatively inexpensive.
- Additionally, the electrode surface is well suited for non-stick welding applications.
- Graphite electrodes offer a high level of energy efficiency and a low cost of production. They can withstand temperatures up to 3000 degrees Celsius, which makes them ideal for use in hot environments such as the engine compartment or undercarriage of vehicles.
- Finally, they have a long lifespan and can be reused many times without experiencing degradation in performance or quality.
To Sum Up
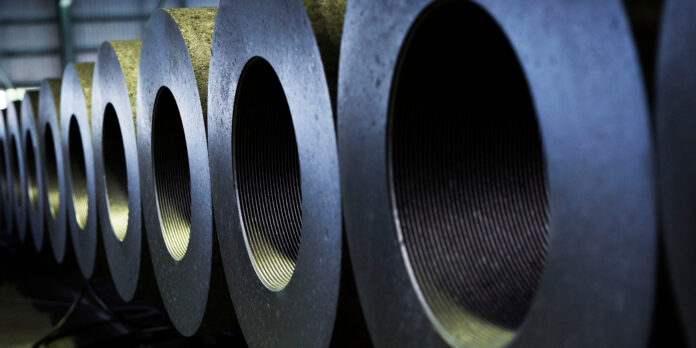
Graphite electrodes are a versatile and powerful material used in many different industries, from steel production to glass manufacturing and the automobile industry.
They offer many advantages over traditional electrode materials, such as being corrosion resistant, energy efficient, and durable, making them an ideal choice for those looking to reduce costs or increase productivity. Furthermore, they can be used in a variety of applications depending on the needs of the industry.