Efficient operations form the backbone of every successful manufacturing plant. Striving for optimal performance involves reducing waste, boosting productivity, and maintaining consistent quality.
One way to ensure this goal is met is through production monitoring systems. By utilizing real-time data to track key metrics, manufacturers gain the insight they need to stay competitive and deliver high-quality results.
In this article, we’ll discuss how production monitoring systems improve manufacturing efficiency.
Key Points
- Real-time data improves decision-making
- Reduced downtime leads to better performance
- Accurate tracking minimizes production errors
- Systems identify inefficiencies early
- Enhanced resource management boosts cost-efficiency
Real-Time Production Monitoring for Informed Decisions
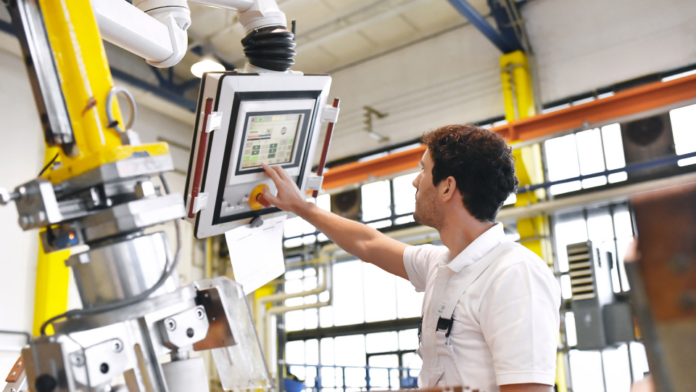
One of the key benefits of a production monitoring system lies in its ability to offer real-time insights. When integrated with manufacturing execution software, a production monitoring system provides up-to-date data on all operations.
This system helps manufacturers monitor processes and make decisions based on reliable information.
A manufacturing execution system is a dynamic software solution designed for real-time production monitoring, helping manufacturers track operations efficiently and improve decision-making. You can draw insights from technologies like those offered by ProManage, a company specializing in manufacturing operations management.
Real-time data ensures that any issues, such as bottlenecks or machine failures, get noticed immediately. Corrective action can be taken quickly, saving both time and resources. It’s about turning data into actionable insights.
Reduced Downtime for Better Performance
Downtime, whether planned or unplanned, can severely affect productivity. Monitoring systems reduce downtime by enabling predictive maintenance. These systems gather data on machine conditions, identifying potential breakdowns before they happen.
Through this proactive approach, manufacturers can schedule repairs at the most convenient times, minimizing the impact on production schedules.
By analyzing patterns in machinery performance, predictive algorithms can suggest when maintenance is required. As a result, downtime gets reduced, productivity increases, and manufacturing efficiency improves.
Improved Accuracy in Production
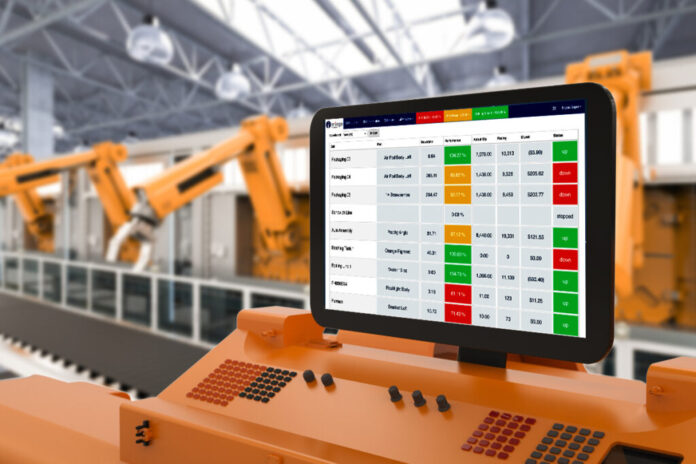
Manual oversight leaves room for human error. Production monitoring systems address this challenge by automating data collection and analysis. Systems accurately record cycle times, machine status, and other critical factors. As a result, errors due to oversight or miscommunication are minimized.
This accuracy extends to managing inventories as well. Real-time data ensures that raw materials are never over- or under-stocked, and finished products are delivered on time. Through detailed tracking, manufacturers prevent shortages and overproduction.
Identifying Inefficiencies Early
Problems like slow production cycles, excess waste, or inconsistent quality can go unnoticed without continuous monitoring. Implementing imaging solutions such as Machine Vision Cameras can enhance monitoring by providing real-time visual data that helps detect inefficiencies early, allowing corrective measures to be implemented before they escalate into larger problems.
When inefficiencies are identified, managers can immediately adjust resources, schedules, or processes. This agility translates into significant cost savings.
Resource Optimization for Cost-Efficiency
Manufacturing companies often struggle with resource management, especially when scaling operations. Effective monitoring systems allow better allocation of resources, including labor, materials, and machinery.
By tracking each asset in detail, companies can ensure that every resource is used efficiently.
Partnering with providers that offer Custom Glass Cutting Services can further enhance resource efficiency by reducing material waste and ensuring components are cut to precise specifications.
This results in reduced waste, lower operational costs, and better overall performance.
The Role of Analytics in Decision-Making
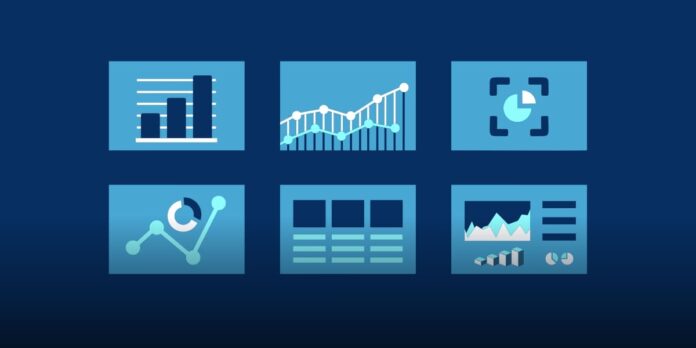
Analytics are the driving force behind many modern monitoring systems. Data collected through sensors and machines is processed into actionable insights that guide management decisions.
By analyzing production data, manufacturers can also forecast future demands, schedule resources accordingly, and maintain a smooth workflow. This data-driven approach boosts efficiency while also enhancing decision-making at every level of the organization.
Greater Agility for Changing Markets
In today’s competitive environment, manufacturers must adapt to changing market demands quickly. Production monitoring systems offer the agility required to respond to fluctuating orders, raw material availability, or customer needs.
By automating many aspects of operations, manufacturers can scale production up or down without sacrificing quality. Monitoring systems also ensure that all processes remain efficient, even when unexpected changes occur.
The Shift Toward Smart Factories
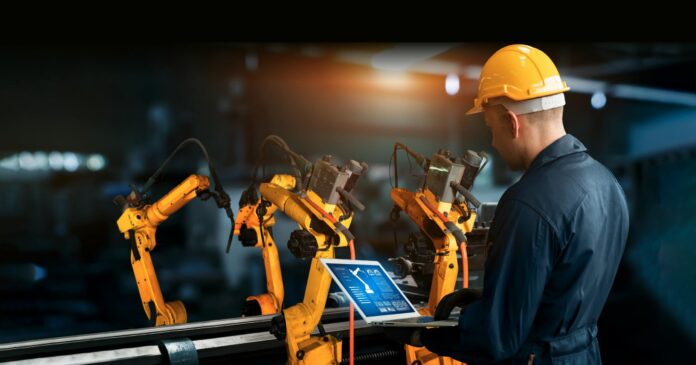
Manufacturing operations are increasingly moving toward smart factory models. This shift involves integrating advanced technologies such as AI, IoT, and augmented reality into everyday operations.
Smart factories represent a step forward in manufacturing efficiency, offering automated workflows, advanced monitoring, and more connected operations. By embracing smart technologies, manufacturers can improve production processes while reducing costs and increasing output.
Conclusion
Production monitoring systems revolutionize how manufacturers manage operations, leading to increased efficiency, reduced waste, and greater agility. Real-time data allows for quick decisions, while predictive maintenance keeps machines running smoothly.
By implementing effective monitoring systems, manufacturers position themselves for long-term success in a highly competitive market. The benefits are clear: better performance, lower costs, and more flexible operations.
Through improved resource management and predictive technologies, manufacturing efficiency continues to evolve, pushing the boundaries of what’s possible.