Finding the right Manufacturing Execution System (MES) can be like choosing the perfect smartphone. You’re looking for something that does more than the basics, doesn’t eat up all your resources, and makes life smoother. But the stakes are even higher here—you’re looking for a tool that could make or break efficiency, productivity, and transparency in operations.
In this article, we’ll walk through essential factors to keep in mind when selecting the right system for your operations. From software compatibility to the user experience, let’s get to what matters so you can make an informed decision.
Key Points
- Focus on compatibility with existing tools and software.
- Check for scalability in future-proofing your choice.
- Look into real-time data visibility.
- Consider security and data compliance.
- Weigh costs against long-term benefits.
Why is the Right MES Essential?
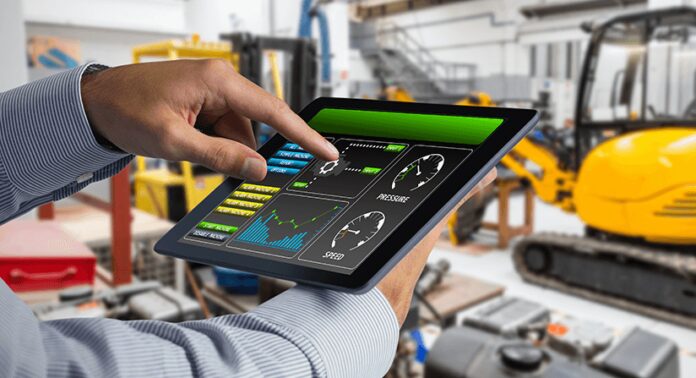
An MES isn’t just some tech that tracks what’s happening on a production line. It’s the nerve center of operations, keeping you informed and making data-driven decisions possible. The best MES offers instant insights and helps manage resources, reducing waste and delays.
Think of an MES like your favorite assistant who knows what’s happening before you do, giving you that perfect nudge just when it’s needed.
Know Your Needs and Goals
When starting, keep in mind that not all MES tools fit every operation. Start by defining the primary goals you want the system to achieve. Are you aiming for improved quality control, or is resource management your top priority?
A solid MES consultant can guide you in this initial phase, helping match your needs with the right system. ProManage’s MES consultants specialize in Manufacturing Operations Management, combining IIoT, AR, and AI to streamline manufacturing processes and boost efficiency.
Key Features to Seek
Every system comes with its bells and whistles, but what do you really need? Here are some essential features that could make all the difference:
- Data Collection: Real-time data on production, labor, and materials is essential. You want insights as things unfold, not days or weeks after.
- User-Friendly Interface: A complex interface can lead to unnecessary delays and mistakes. The best systems are intuitive, making it easier for operators and managers alike.
- Data Integration: Check if it works well with the other tools in your setup. Nothing’s worse than having data you can’t even connect to your reporting tools.
- Flexible Reporting: Look for customizable dashboards and reports. They should help track progress and spot problems quickly.
Real-Time Data Visibility
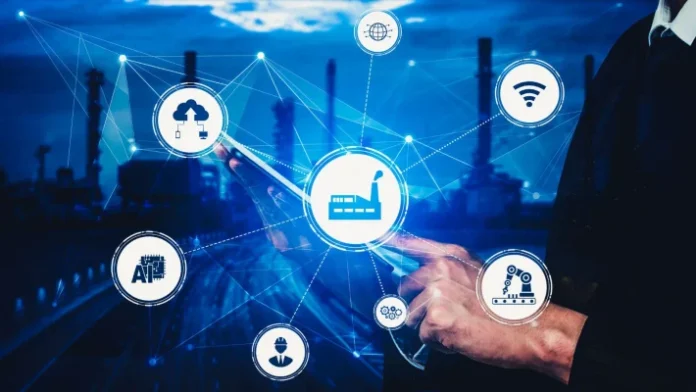
Imagine seeing everything in your operations as it happens. An MES with real-time data offers that advantage.
It gives you a full view of the current situation, so you know where resources are going, the status of equipment, and can even detect issues before they snowball into bigger problems. When every second counts, real-time tracking is a lifesaver.
Checklist: Is Your MES Covering the Essentials?
- Does it offer real-time updates?
- Can it integrate smoothly with existing systems?
- Does it allow remote access for off-site management?
- Are its analytics tools customizable?
- Is it scalable to match growth?
Security and Compliance
MES tools often handle sensitive data, making security a non-negotiable aspect. Choose a system that prioritizes data protection and complies with relevant standards. Good systems come with encryption, regular updates, and user access control.
The importance of security here isn’t just about preventing cyber threats. It’s also about ensuring that only the right people access critical data.
Scalability for Long-Term Success
An MES should not just serve current needs. It should be able to handle your growth over the next 5, 10, or 20 years. Choosing a scalable system means you won’t have to start over from scratch when operations grow. Ideally, it should support new functions, adapt to changing requirements, and grow with your business.
Tips for Ensuring Scalability
- Look for modular solutions you can expand as needed.
- Check for compatibility with future updates.
- Consider whether it supports multi-site management.
Cost vs. Value: What Are You Really Getting?
It’s easy to think of an MES as a hefty expense, but look closer. The right choice isn’t about finding the cheapest option—it’s about finding one that delivers the most value. Remember, a quality system could reduce manual effort, minimize downtime, and even lower material waste.
Take a practical approach: review the return on investment and measure it against the system’s upfront cost and maintenance.
Training and Support: The Secret Ingredients for Success
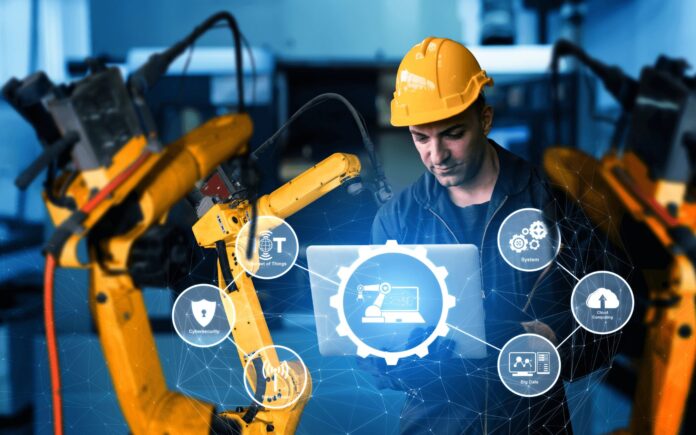
Selecting an MES isn’t just about the software itself. Training and support play important roles in ensuring it actually works for your operation. The most advanced system in the world won’t help if your team can’t use it effectively. Training should cover not only basic usage but also troubleshooting, system updates, and data interpretation.
Look for a provider that offers comprehensive support—ideally with resources like dedicated helplines, on-site assistance, and online resources. Quality support isn’t just an add-on; it’s essential for maximizing the value of your MES.
Investing in a system with robust support and a solid training program will empower your team and enhance productivity from day one.
FAQs
1. What if my MES doesn’t integrate with my other software?
Some MES tools offer integration solutions, but if it’s a complete mismatch, it might be time to reconsider either the software or the MES. Compatibility is key.
2. How much training does the average MES require?
It varies, but most take between a few weeks and a few months for full training, depending on the complexity.
3. What level of customization can I expect?
Most systems offer a basic level of customization, such as dashboards and reports. Advanced customization often depends on your provider.
4. Are cloud-based MES solutions better?
Cloud-based options offer easy access from anywhere, reduced hardware costs, and frequent updates. However, they require reliable internet.
5. Can MES improve overall productivity?
Yes, a well-implemented system provides better resource management, quality control, and real-time data, often leading to productivity gains.
Conclusion
Choosing the right MES might feel overwhelming, but by focusing on your actual needs, the importance of scalability, and solid data integration, you can make the process smoother.