Packaging plays a crucial role in the journey of a product from the manufacturer to the end consumer. Amidst various packaging solutions, shrink wrapping machines have carved a niche for themselves due to their efficiency and effectiveness.
A shrink wrapping machine, essentially, wraps a product in a loose sleeve of plastic film, which is then heated to condense tightly around the item. This technology is not just about encasing a product; it’s about precision, product protection, and presentation.
Exploring the Spectrum of Shrink Wrapping Machines
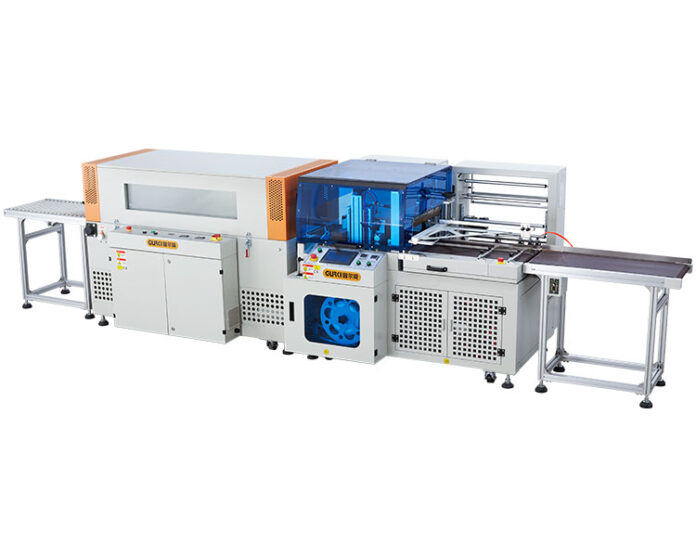
When delving into the world of shrink wrapping machines, one encounters a variety of options, each suited to different needs and scales of operation. Manual, semi-automatic, and automatic wrapping machines form this spectrum. Manual machines are hands-on and cost-effective, perfect for small-scale operations.
Semi-automatic variants offer a middle ground, where some part of the process is automated, balancing efficiency with control. The automatic machines, although a significant investment, are a boon for high-volume packaging, drastically reducing human labor and ensuring uniformity.
The Mechanics of Shrink Wrapping Machines
The magic of shrink wrapping machines lies in their simplicity and effectiveness. The process generally involves three stages: sealing, shrinking, and cooling. Initially, the product is enveloped in film, which is then sealed to form a loose bag around the item.
The sealed item passes through a heat tunnel, causing the film to contract snugly around the product. Finally, the package is cooled to strengthen the film’s material properties, ensuring a tight, tamper-proof seal. To see the best way this technique is applied visit Phoenix Handling Solutions.
Advantages of Shrink Wrapping Machines
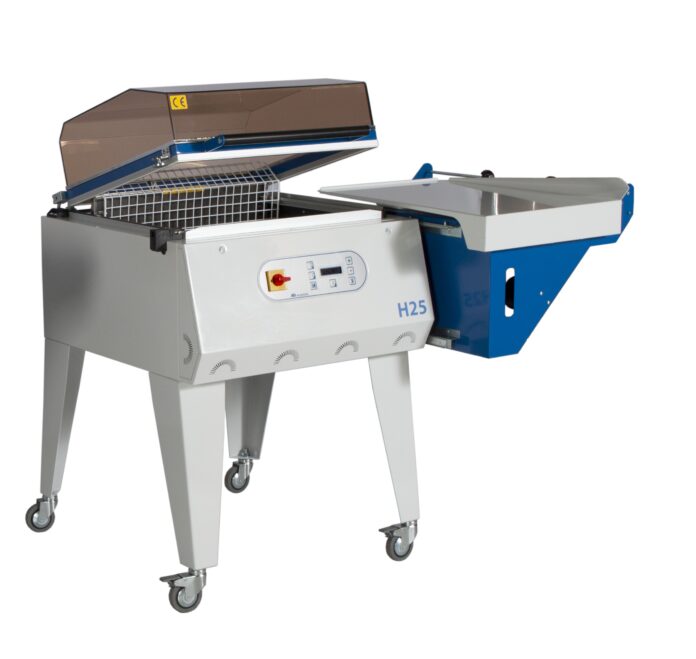
Shrink wrapping machines bring a host of benefits. They enhance product aesthetics, ensuring a clean, professional look that resonates with consumers.
The tamper-evident nature of shrink wrapping adds a layer of security, safeguarding against contamination or tampering. From an operational standpoint, these machines contribute to significant efficiency gains. They automate the packaging process, reducing labor costs and minimizing errors.
Maximizing fficiency in Shrink Wrapping
Efficient packaging is not just about having the right machine; it’s also about optimizing its usage. Selecting the appropriate machine and setting it up correctly is fundamental.
The choice of shrink film is crucial too; it should be compatible with the product and the machine.
Fine-tuning the heat and settings is essential to achieve the perfect wrap without damage to the product. Regular maintenance and adherence to safety guidelines ensure the longevity of the machine and the safety of the operators.
Avoiding Pitfalls in Shrink Wrapping
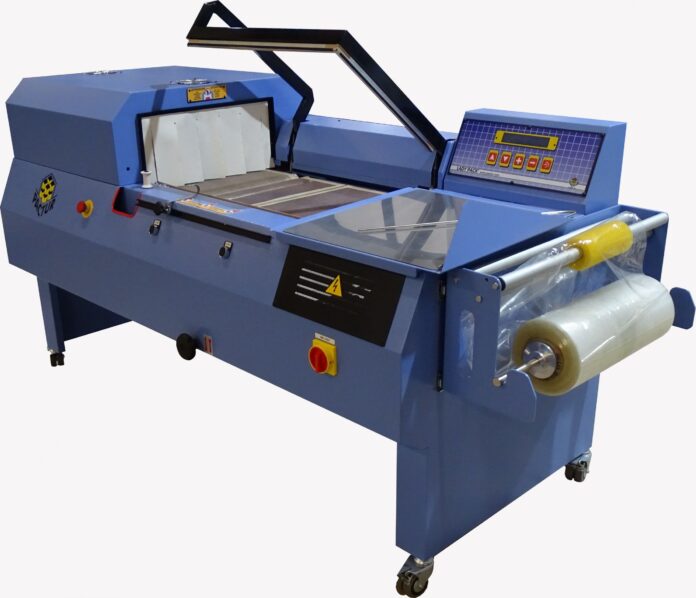
Every technology has its learning curve, and this wrapping is no exception. Common issues like uneven shrinkage or film tears can mar the packaging’s look and integrity.
Understanding the machine’s functioning, selecting the right materials, and regular maintenance are key to avoiding these pitfalls. When issues arise, a systematic troubleshooting approach can save the day, preventing minor issues from escalating into major setbacks.
Shrink Wrapping Across Industries
Shrink wrapping’s versatility shines across various industries. In food packaging, it keeps items fresh and protects them from contamination. Retailers rely on this wrapping for its aesthetic appeal and tamper-evident features.
Industrial sectors appreciate the durability and protection it offers for goods in transit. Numerous success stories attest to its role in enhancing product appeal, ensuring safety, and streamlining operations across these sectors.