When it comes to modern manufacturing, efficiency and precision are no longer luxuries – they’re non-negotiable. That’s where the robot welder steps in.
Once considered a futuristic novelty, robotic welding systems are now a practical and cost-effective solution for businesses looking to boost productivity and reduce human error.
What Is a Robot Welder?
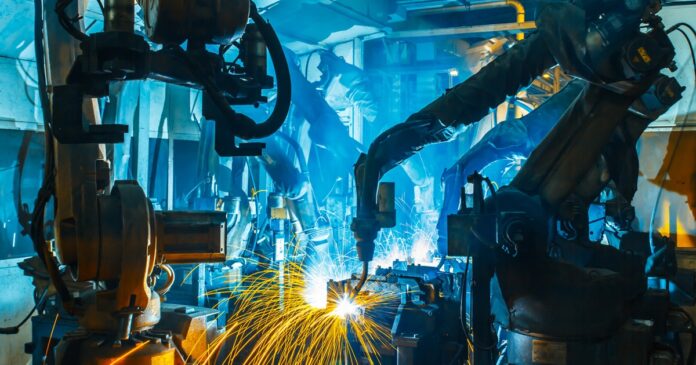
A robot welder is an automated system programmed to perform welding tasks with speed and consistency. These machines are typically used in high-volume production environments, like automotive or structural steel manufacturing, but they’re becoming increasingly accessible to smaller workshops too.
With advanced sensors, multi-axis arms, and AI-guided precision, robot welders can execute complex welding jobs with a level of accuracy that’s hard to match manually.
Whether it’s MIG, TIG, or spot welding, these systems are designed to deliver clean, repeatable welds at high speeds.
Newer models also feature real-time monitoring capabilities, enabling operators to track weld quality and system performance on the go. This integration with data analytics allows businesses to identify inefficiencies early and make continuous improvements.
Why Businesses Are Investing in Robotic Welding
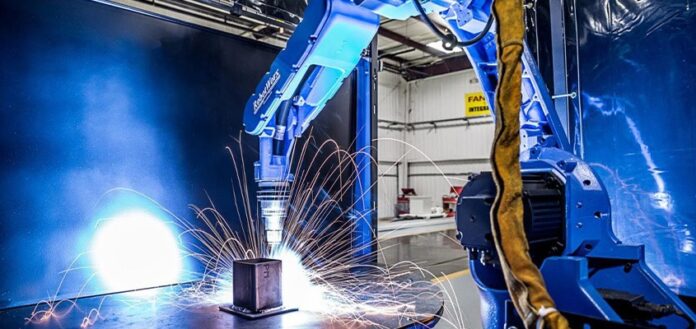
The initial investment in robotic welding can seem steep – but the long-term return is undeniable. Here’s why more businesses are making the switch:
Increased Productivity: Robot welders don’t need breaks, shift changes, or rest days. They can operate around the clock, drastically increasing output.
Consistent Quality: Human welders, no matter how skilled, can introduce inconsistencies. Robots remove variability, ensuring every weld meets exact specifications.
Workplace Safety: Welding is a hazardous task. By automating it, you reduce exposure to heat, fumes, and arc flashes, protecting your workforce.
Cost Savings: Over time, the savings in labour, materials (thanks to reduced waste), and faster project completion often outweigh the upfront cost of the robot itself.
Companies also benefit from a reduction in rework, which can be a major cost factor in manual welding environments. The enhanced accuracy of robotic systems helps minimize these costly errors.
Is a Robot Welder Right for Your Business?
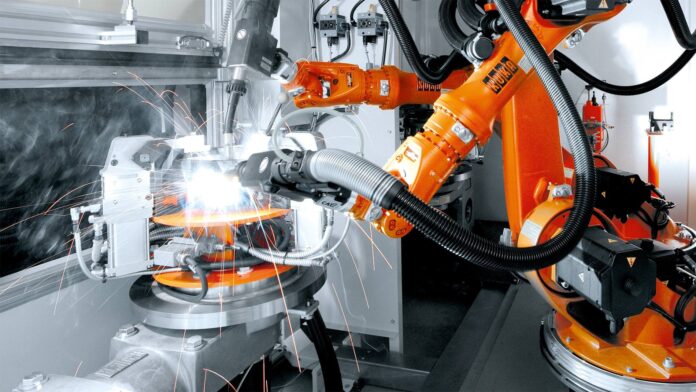
If you’re handling repetitive welds or looking to scale your operations, the answer is likely yes. Even in custom fabrication, modern robot welders can be reprogrammed quickly to adapt to different parts and welding techniques.
However, robotic welding isn’t a replacement for skilled welders – it’s a tool to enhance their output. Many companies use robots for the repetitive work, freeing up human welders for more complex or creative tasks that require a craftsman’s eye.
Investing in training for your team to work alongside these machines can also improve operational efficiency and employee satisfaction.
The Future of Welding Is Here
As technology continues to evolve, so does the versatility and affordability of automated solutions. With more options on the market than ever before, now could be the perfect time to explore how a robot welder could transform your business.
Whether you’re a fabrication shop, a car manufacturer, or a small engineering firm, embracing automation could be the edge you need to stay competitive in an increasingly demanding market.