Maximizing warehouse space is not optional when dealing with large, heavy, or oddly shaped inventory. You need structure and strategy. Poor racking choices lead to damage, delays, and lost productivity. The right racking system, on the other hand, transforms chaos into order. It gives you control over space, simplifies access to goods, and improves safety for everyone involved.
This guide covers the most effective racking solutions for bulky warehouse items. It focuses on strength, layout adaptability, and material flow optimization—without wasting space.
1. Cantilever Racks for Oversized, Irregular Inventory
Cantilever racks are built for long, heavy, or bulky materials. Pipes, lumber, sheet metal, steel bars, and furniture frames don’t fit into traditional pallet rack configurations. You need support arms—not pallets—to handle those loads.
Cantilever systems rely on upright columns and adjustable arms that extend outward to carry the weight of items that would otherwise sprawl across the floor. They offer open-front access and flexibility for both length and height.
For those handling wide-span or heavy structural items, the warehouse racking system at Speedrack West offers a structural I-beam construction with either 12 ft or 16 ft uprights. You can choose between single-sided or double-sided configurations depending on your space and handling needs.
Key benefits:
- Clean access without vertical obstructions.
- High weight capacity per arm.
- Custom spacing based on load length.
- Adaptable to warehouse layouts and ceiling heights.
2. Pallet Racking for High-Volume, Uniform Inventory
If your warehouse relies on forklifts, standardized pallet sizes, and high inventory rotation, pallet racking is your backbone. This system supports heavy loads across multiple vertical levels and allows for simple loading and unloading with equipment.
You can design pallet racks with narrow aisles for space savings or wider access lanes for faster movement. Beam levels adjust easily, and safety bars or wire decking can be added for load support. For even greater adaptability, select racks that offer boltless assembly or heavy-duty steel frames.
Best uses:
- Manufacturing and distribution centers with packaged goods.
- Inventory where FIFO or LIFO methods apply.
- Locations with dedicated forklift lanes and lift access.
Different configurations:
- Selective pallet racking (standard and most flexible).
- Double-deep racking (for increased density).
- Pallet flow racking (for high-throughput FIFO systems).
3. Push-Back Racks for Depth and Quick Restocking
When you need to store multiple pallets of the same SKU in a limited footprint, push-back racking offers a smart solution. These systems use gravity rollers or carts that push backward as new loads are added. It’s a Last-In, First-Out (LIFO) setup—ideal for products with stable shelf life and frequent stock movement.
Unlike drive-in racks, push-back models allow multiple SKUs in a single aisle run. Each level operates independently, which minimizes the risk of damaging other pallets during loading.
Advantages include:
- Higher density than selective pallet racks.
- Faster loading since forklifts do not need to enter the rack.
- Better stock rotation control for certain categories.
Ideal applications:
- Beverage warehouses.
- Packaged food.
- Home improvement goods.
4. Drive-In Racks for Maximum Density
For warehouses with limited floor space but large inventories of the same item, drive-in racks maximize every inch. These systems eliminate aisles by allowing forklifts to enter the racking structure itself and place pallets directly on rails.
They use a single loading/unloading path, operating on a LIFO basis. Although access is more limited, the storage density is unmatched. Drive-in racks are best when you don’t need constant pallet rotation and where large volumes of the same SKU dominate your inventory.
Design tip: Always assess your forklift clearance and turning radius before installing drive-in systems. Safety accessories like guide rails and bumpers are not optional.
Used in:
- Cold storage warehouses.
- Seasonal product storage.
- Bulk-item distribution hubs.
5. Heavy-Duty Shelving for Non-Palletized Loads
Not every heavy item fits on a pallet. Some tools, dies, containers, or machine components require more surface area or direct hand access. Heavy-duty shelving provides a flat surface with high load tolerance and easy reach.
These units support anywhere from hundreds to thousands of pounds per shelf and can be built with adjustable steel levels, mesh decking, or solid wood panels. Shelving often works best at ground level or for mezzanine-supported systems where product handling is done manually.
Where it works:
- Maintenance workshops.
- Tool cribs.
- Small-parts storage.
Shelving gives you flexibility. You can mix drawer cabinets, bins, or open levels depending on the nature of your inventory. It’s not as space-efficient as palletized storage, but it’s essential for control and organization in hands-on environments.
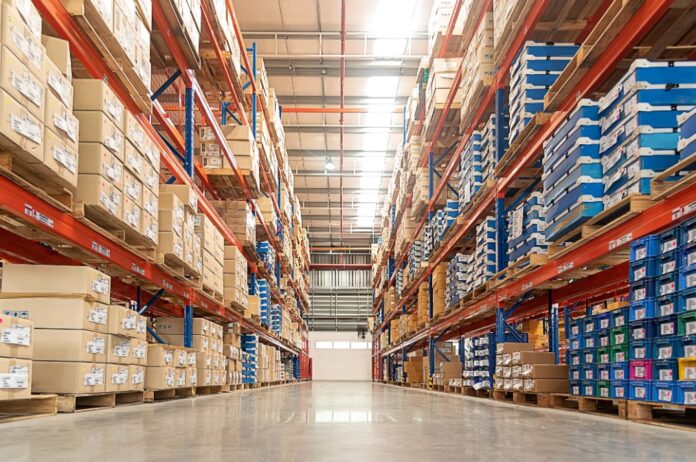
6. Mezzanine Racking – Stack Vertically Without Structural Overhaul
When you’ve run out of horizontal space and need a solution without costly building expansion, mezzanine racking creates an upper level for storage, office use, or assembly areas. It’s a steel platform installed within your warehouse, fully independent of the building structure.
In many cases, racking can be built directly under the mezzanine. This dual-purpose setup increases cubic storage dramatically.
Use mezzanines when:
- Floor-level space is full, but ceiling height is underutilized.
- Operations need division between heavy inventory and light assembly.
- Temporary or modular upgrades are preferred over new construction.
Features to consider:
- Load-bearing capacity per square foot.
- Access via stairs, gates, or lifts.
- Customization for lighting, flooring, and handrails.
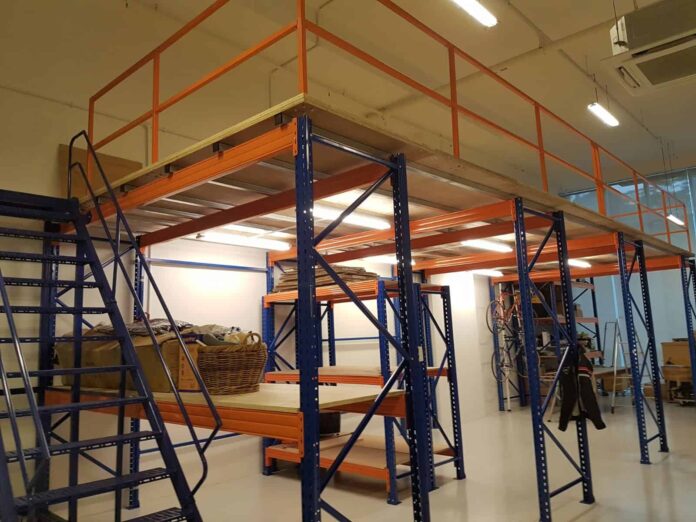
Conclusion
Heavy and bulky items don’t have to overwhelm your space. With the right system—whether cantilever, pallet, push-back, drive-in, or mezzanine—you can expand your capacity, streamline picking, and improve safety. Storage is not just about stacking things higher. It’s about smarter design, proper weight distribution, and ease of access.
Evaluate your inventory flow, floor plan, and handling equipment before choosing a racking layout. Build for the load you have today and the scalability you’ll need tomorrow.
An efficient warehouse begins with the right structure. Invest in storage that supports your business—not one that holds it back.