Choosing the right gas for your laser cutting operation can make or break the process. Nitrogen and oxygen are the top choices, but how do you know which gas is better for your specific needs? It’s not a one-size-fits-all situation. The material, the cut quality you want, and even your production goals all play a role in this decision.
Let’s break down how each gas affects the laser cutting process and give you the information to make the right choice.
Key Points
- Nitrogen creates clean, oxidation-free cuts.
- Oxygen produces faster cuts but leaves oxidation marks.
- The choice depends on material, speed, and precision needs.
- Cost of gas and operational efficiency also impact the decision.
The Role of Nitrogen in Laser Cutting
1Nitrogen is typically used when a clean, oxide-free cut is critical. Stainless steel, aluminum, and other non-ferrous metals benefit from nitrogen. By forming a protective atmosphere, nitrogen prevents oxidation on the edges of the cut. This ensures a clean and shiny edge without discoloration.For continuous cutting operations, a nitrogen generator can ensure that your nitrogen needs are met efficiently. Companies like Berg Gasetech provide nitrogen generator laser cutting solutions that help optimize gas supply, cutting down on operational costs.
Laser cutting with nitrogen produces results that are aesthetically superior. You often see this with parts requiring minimal post-processing. The gas effectively cools the cutting area, reducing the risk of melting or deformation in delicate materials.
The Impact of Oxygen in Laser Cutting
Oxygen works differently. It reacts with the metal, actually speeding up the cutting process. The reaction between oxygen and the material creates heat, allowing for faster cuts in thicker materials like mild steel. Oxygen cuts are typically used when speed is more important than precision.
However, oxygen leaves oxidation on the edge of the cut. The finish will often appear rougher or discolored, but this is usually acceptable for structural components or parts that don’t need a polished finish.
The trade-off with oxygen is its speed versus finish. For high-throughput environments where time is a key factor, oxygen offers an advantage. It’s faster and can handle thicker materials more effectively than nitrogen.
Material Considerations
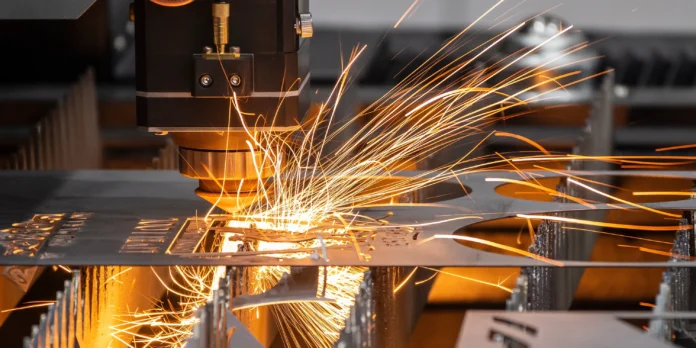
Choosing nitrogen or oxygen largely depends on the material you are working with. For non-ferrous metals like aluminum and stainless steel, nitrogen will give you cleaner cuts. You will avoid the discoloration and oxidation that often appear with oxygen.
On the other hand, oxygen excels at cutting thicker, ferrous metals like mild steel. The added heat from the reaction speeds up the process, making it ideal for those needing fast throughput.
One gas may be better for thin, delicate metals while the other excels in thick, rugged materials. It’s crucial to consider how the metal will be used in the end product when selecting a gas.
Speed vs. Quality
If you prioritize speed over quality, oxygen is the better choice. The added heat from the oxygen reaction reduces the amount of laser power needed to cut through thick materials. This allows you to move faster without increasing your laser’s power.
However, if cut quality and finish are non-negotiable, nitrogen is the better option. It may take longer to cut, but you’ll get a much cleaner result. The lack of oxidation means no need for secondary processes to clean up the edges.
Your choice depends on what you prioritize—time or quality.
Costs and Efficiency
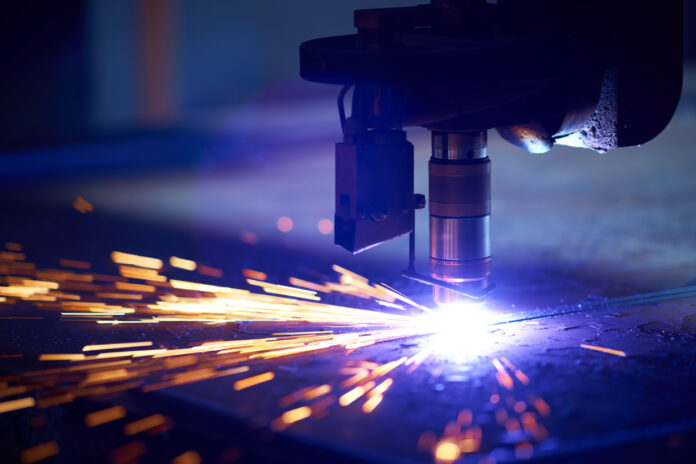
Nitrogen tends to be more expensive because you use it in higher volumes to create the inert atmosphere needed for clean cuts. However, using a nitrogen generator can bring down costs significantly by eliminating the need for constant refills.
Oxygen, on the other hand, requires less volume but adds costs in other areas. You may need more post-processing to clean up oxidized edges, which adds time and labor to the project.
Balancing operational costs with production goals should be part of your decision-making process. A clean cut may save time later in the process, while a fast cut may save money upfront but require more post-cut handling.
Safety and Maintenance
Oxygen, because of its reactive nature, poses more risk than nitrogen. Using oxygen increases the risk of fire or explosion, especially if there are any oil or grease contaminants in the system.
Nitrogen, being inert, is much safer to handle. It won’t react with the material or the environment, reducing the overall risk in the workplace.
Oxygen systems often require more attention due to their reactive nature. Regular inspections are necessary to ensure that contaminants don’t enter the system, which could lead to dangerous situations. Nitrogen systems generally require less maintenance.
The Bottom Line: Nitrogen or Oxygen?
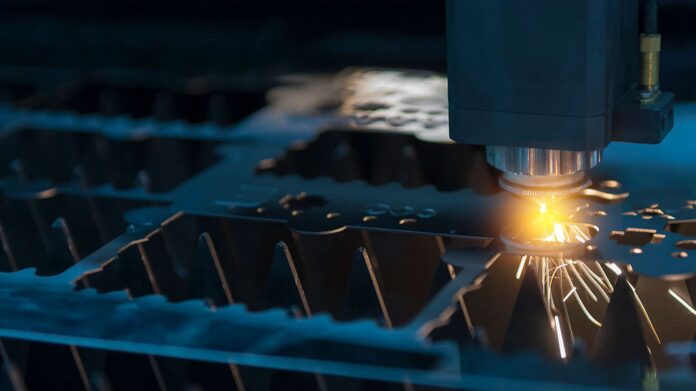
To decide whether nitrogen or oxygen is better for your needs, you need to consider several factors.
- What materials are you cutting?
- Do you need a fast process, or is a clean finish more important?
- What is your budget for gas and operational costs?
- Are you concerned about safety and maintenance?
If you’re cutting non-ferrous metals and need a clean, polished finish, nitrogen is your go-to choice. It will give you an oxidation-free cut with minimal post-processing. The higher gas costs can be mitigated by investing in a nitrogen generator, ensuring you always have a reliable gas supply.
Oxygen, on the other hand, is ideal for those cutting thick, ferrous metals where speed is critical. The oxidized edges may not matter if the final product doesn’t require a clean finish. Oxygen’s lower gas costs can also make it more appealing for operations that don’t prioritize edge quality.
When to Choose Nitrogen:
- Cutting stainless steel, aluminum, or other non-ferrous metals.
- When a clean, oxidation-free finish is crucial.
- For precision cuts that require minimal post-processing.
- If safety and reduced maintenance are key priorities.
When to Choose Oxygen:
- Cutting thick, ferrous metals like mild steel.
- When speed and efficiency outweigh the need for a clean finish.
- For high-volume production where throughput is important.
- If operational costs are a higher concern than cut quality.
Final Thoughts
Also read: CNC Cutting Machines
Both nitrogen and oxygen play essential roles in laser cutting, but they serve different purposes. Your choice should reflect your specific needs—whether that’s speed, material type, cut quality, or safety.
The wrong gas can slow down your operation, increase costs, or affect the quality of your final product. But with the right gas choice, your laser cutting process will run more smoothly and efficiently.