The efficiency and safety of pneumatic systems implies the selection of appropriate connections for air hoses. That is key. These fittings, especially the quick-connect type, allow a quick and secure connection between hose and pneumatic tools or air supply, drastically reducing downtime and improving productivity.
The variety of shapes, sizes and materials available can create confusion when choosing. That’s why you need to carefully determine your needs in order to make the right choice. For more information check air hose quick connect options..
Watch out for compatibility
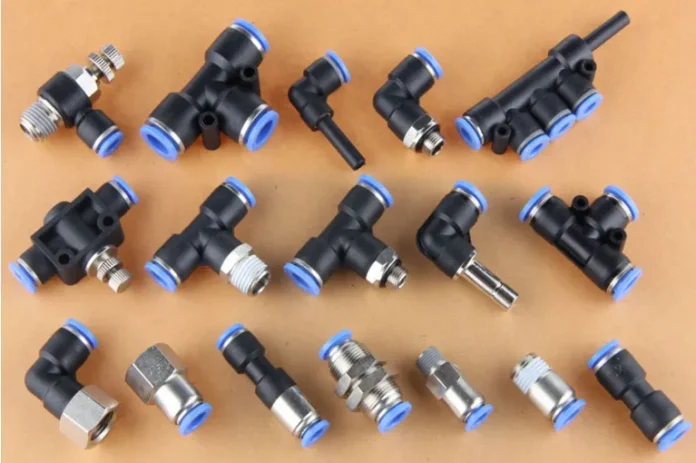
The first thing you need to do when choosing air hose fittings is to make a good connection. That is, compatibility. The quality is worthless if the fittings are not correct and if the size and type of your air hose and tool do not match.
Improper connections can lead to leaks, reduced performance, or even damage to your equipment. Standard sizes include 1/4 inch, 3/8 inch, and 1/2 inch, which refer to the diameter of the hose or fitting. Each size corresponds to different levels of airflow and pressure, which are determined by the tools you intend to use.
How does an air hose quick connect work?
Inside the fitting end of the hose and the tool end where it connects, there’s this part called a collet. The collet has these little teeth all around the inside. When you push the hose onto the tool, air or water gets pumped in and the pressure forces the collet to squeeze in tight.
As the collet squeezes in, it falls into a groove cut into the fitting. Think of it like sinking your teeth into a grilled cheese – the groove traps the collet teeth in place.
Now here’s the cool part. All that pressure squeezing the collet and those teeth digging into the groove makes it almost impossible for the hose to come loose! The connection is super secure.
Brass, steel or plastic?
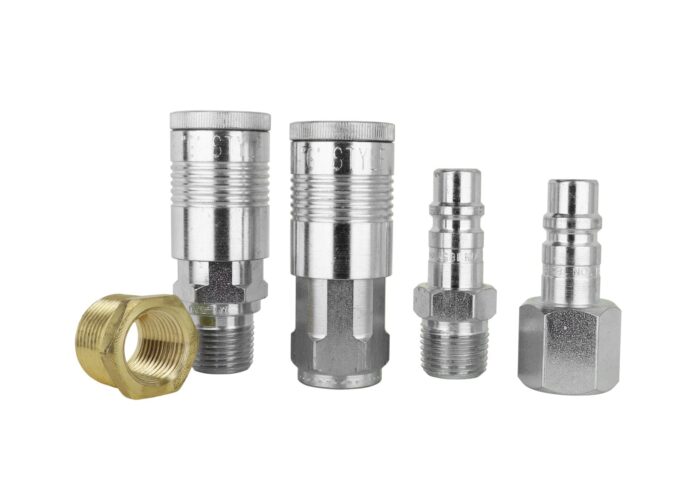
The material the air hoses are made of is another key consideration. Common materials include brass, steel, stainless steel and plastic. Each of them has its advantages and disadvantages. Brass is resistant to corrosion and is commonly used for its durability and affordability. Brass is basically a two-component alloy of copper (Cu) and zinc (Zn).
In order to improve the properties of brass, such as workability and corrosion resistance, other chemical elements are added in smaller quantities, and in this way “special brasses” are obtained.
It can be said that the best mechanical properties are achieved at a zinc content of about 40%. The addition of zinc increases the tensile strength of brass and decreases electrical and thermal conductivity.
Steel fittings are stronger and ideal for high-pressure applications. Steel pipes in this quality are used if the maximum temperatures are up to 70 C. Stainless steel offers the best corrosion resistance and is suitable for harsh environments.
Does the plastic is option?
Plastic air pipes are inexpensive, corrosion-resistant and easy to install. However, there are some contraindications for their use in compressed air distribution:
Not all plastic pipes are suitable for the distribution of compressed air. The use of PVC pipe in any compressed air application is extremely dangerous and is not recommended by several associations and manufacturers.
When air is compressed inside a PVC pipe, the pipe can swell and explode under high pressure, releasing PVC debris in an uncontrolled manner.
This type of pipe also deteriorates and becomes brittle over time, increasing the possibility of leaks or explosions as it ages.
Its use can result in OSHA (Occupational Safety and Health Administration) violations for both compressed air and gas transportation.
Study the specifications
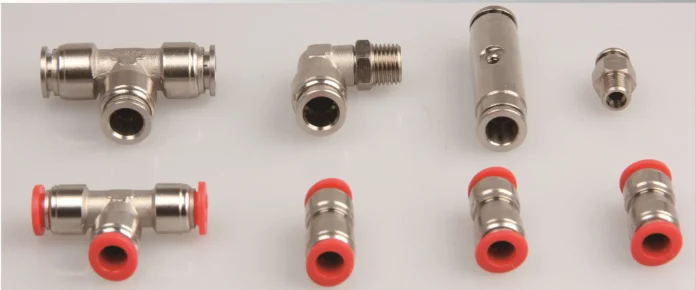
The operating pressure and flow of your pneumatic system also significantly affects the choice of quick connect fittings. It is vital that you choose fittings that can handle the maximum pressure and flow rate of your system to avoid failure. Typically, manufacturers specify maximum pressure and recommended flow rates for their fittings. Make sure these specifications exceed or meet your system requirements to maintain efficiency and safety.
Environmental factor
Environmental factors such as temperature, humidity, and exposure to chemicals also play a role in selecting appropriate air hose connections. Extreme temperatures can affect the performance and durability of the fitting. For example, plastic parts can become brittle in cold environments, while brass can handle a wider temperature range.
In addition, exposure to chemicals can degrade certain materials faster than others. It is therefore essential that you keep in mind the environmental conditions that your equipment will come into contact with.
Don’t forget about safety
Safety, along with ease of use, is paramount in any pneumatic system, and choosing a fitting with the appropriate safety features is key. Some quick-connect fittings come with locking mechanisms to prevent accidental disconnection, which can be especially important in high-pressure applications or busy work environments. In addition, some fittings are specially designed to release air before disconnection occurs, reducing the risk of hose impact, which is a safety hazard.
Simplicity often comes first
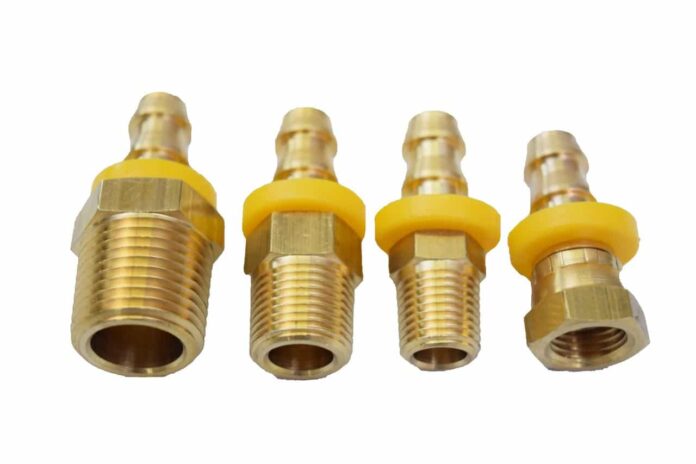
We all like it to be simple and fast, without too much complication. Quick-connect fittings that are easy to connect and disconnect, not only saving time but also reducing wear and tear on tools and hoses. However, you should regularly check for leaks or wear. Opt for fittings that are known for their reliability and ease of maintenance. This will ensure proper operation.
Conclusion
It’s super important to really study the details when picking out hoses. I know specs can seem boring, but they’re key to making sure everything works well together. Take your time reading the instructions – it’ll pay off to understand the material, pressure levels and flow rates the hose can handle.
Think about where and how you’ll use it too. Will it be indoors or out? Do you need safety features? How easy should it connect and disconnect?
Compatibility is huge too. You want hoses that’ll fit all your pneumatic tools perfectly. Talking to experienced folks can really help with that.
The right hoses not only get the job done, but keep you and your gear safe over the long run. Don’t forget about extras like fittings – they’re worth investing in for performance and protection.