Before getting into the topic, it is necessary to know what safety data sheet management is and where it is used. SDS management is a health and safety practice that ensures the safety of people who work in various fields related to chemicals. Generally, the SDS sheet will denote the property of each chemical, the environmental issue, and the hazards of that particular chemical. This information will be useful for people who work with chemical hazards to protect their physical health.
Hence people who work in this field will protect themselves from chemical compounds while transporting, storing, and handling in various situations. In general, it provides in-depth guidelines for people to protect themselves from risks in various situations.
But how does it help? What methods have to be implemented to have a successful safety data sheet management system on your premises? Continue reading this article till the end to know more about tips for improving safety data sheet management. You can visit thesdsfactory.com to know some expert tips on safety data sheet management.
Tips for improving your safety data sheet management
1. Never delay in implementing new ideas:
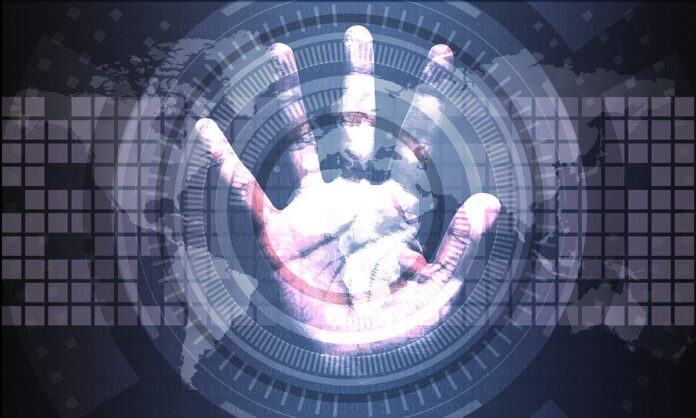
According to the survey and data analysis, it is said that from June 1st, 2015, all the companies in the USA and the countries around the USA are expected to implement the safety data sheet in GHS format to maintain safety and security among the people who work in your company.
The new and updated rules and regulations and safety data sheet management system must be implemented and circulated among all the employees. Appropriate workers in various fields must read the system management sheet to understand and follow the same in their companies.
This system and updated rules will avoid many logistical problems in their company; people can avoid mistakes because of the clear and well-explained new SDS sheet. This is for the manufacturers who produce a wide range of chemicals in huge numbers, but people with small places have already implemented many rules and regulations on their premises.
But most companies are expecting their vendor companies to update the rules to follow the same in their companies. Even companies have received the extended time for implementing the new SDS sheet, so make sure to update the sheet and follow the same in your company to provide your workers with enhanced safety and security.
2. Following OSHA communication standards
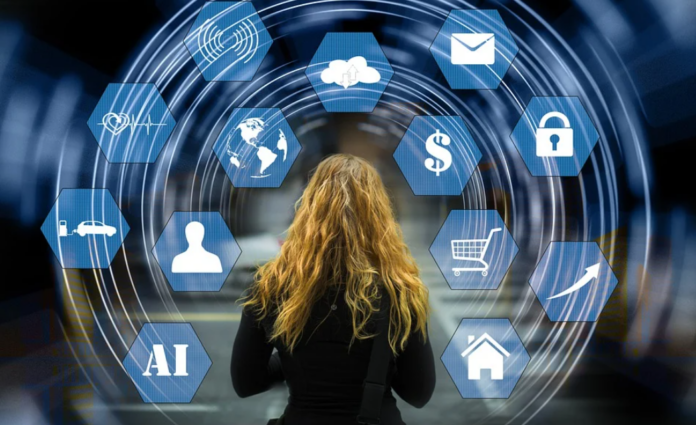
OSHA is organizational safety and health administration which is the same as that of Safety data sheet management. SDS management protects employees and other people from accidents by providing proper guidelines. OSHA is a health and safety protection act that is followed in the USA to provide enhanced safety. Besides safety, it is also responsible for the accidents occurring on all the premises in the USA.
Generally, OSHA has implemented SDS and made them published all over the companies in the USA, so, under the surveillance of OSHA and lab safety standards, SDS must be kept available for all the workers who work in all the shifts. In short, the companies that involve many chemical components and fluids must follow the standards of OSHA; to have a proper OSHA, you must implement SDS standards.
3. Implement some strict rules and allocate a separate team for SDS
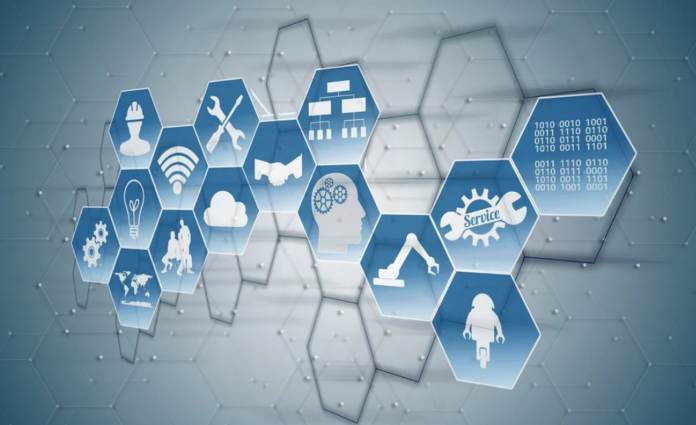
It is better to have a separate supervisor for this team than to have a universal manager or supervisor. OSHA is a wide program, and in order to make the team more powerful and effective, you must allocate a separate manager and two assistant managers to make your team more effective.
This person will take care of all the rules and regulations, and other formalities that OSHA needs. SDS is a main element of OSHA so that the following duties will be under the manager’s control.
• The manager implements all the guidelines as per the requirement of the government.
• Make people understand the guidelines by educating them with proper strategies.
• Should make people follow the guidelines to ensure the safety of all the departments.
• Review the format and implement some changes if there is a need.
• By Conducting regular meetings, people can educate employees about updated rules and regulations. Companies never follow the same rule and prefer to improve the rules and regulations to enhance safety and security.
So having a separate team and a lead for that team can make your premises a danger-free zone. SO make sure that you implement all the rules and regulations with an in charge.
4. Use some SDS tools
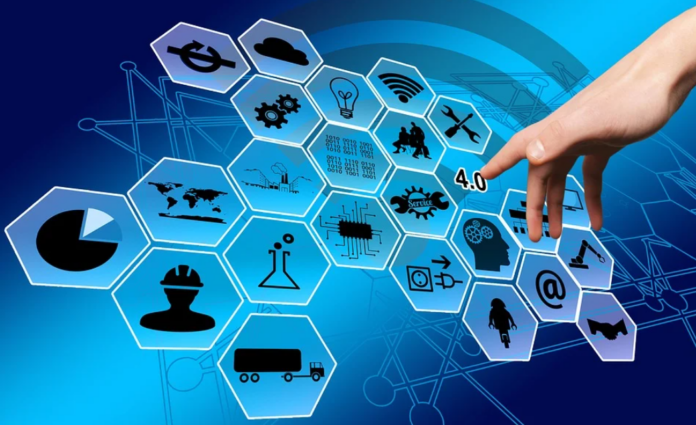
People can find a wide range of tools and applications for managing their companies safety data system. It will be a hectic task for people to maintain a manually written ledger and keep them safe for years, and because of this, we have seen a lot of devices to make the process easy. Even for safety data management, people have many applications.
One such reliable application is three-ring binders where people can get some ideas and recommendations for what to store and when to do it. Cloud-based SDS management has also gained importance worldwide, so this is the trend in today’s situation.
The best electronic system is the one that saves them time and money for that particular company, so an automated system GHS will be made easy by implementing this computerized system in your company. The result will be flagged and filtered according to the category, so make sure you have a computerized system for SDS management.
Final words
Hence in this article, we have seen a detailed review of SDS, and now people must have a clear idea of OSHA and SDS concepts. Enhanced safety in dangerous places is a must, and people from various places prefer to have this system have a formulated system.
This system will make your company work in a better way. Keep in mind that you have to update your employees to keep them updated with the latest safety features. I hope this article has given you some information regarding SDS management! Thank you for reading this article.