Spring steel is a type of steel specifically designed to withstand significant bending or twisting and return to its original shape. It is known for its high yield strength, which means it can endure substantial stress without permanently deforming. This makes it ideal for manufacturing springs and other components that require flexibility and resilience.
But how exactly is spring steel made? Let’s break down the process in an engaging and simple manner that will make even the most complex details easy to understand.
1. Selecting the Raw Materials
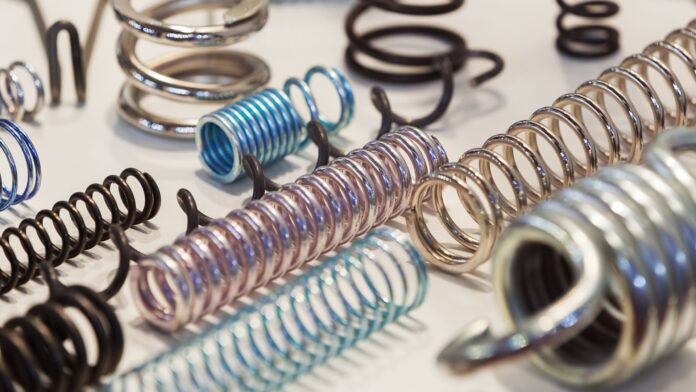
The journey of spring steels begins with the selection of raw materials. High-quality iron ore and carbon are the primary ingredients. The choice of raw materials significantly impacts the final product’s properties, so manufacturers pay close attention to the purity and quality of these inputs.
2. Melting and Refining
The selected raw materials are melted together in a blast furnace at extremely high temperatures. This process removes impurities and combines the iron and carbon to form steel. Depending on the desired properties of the final product, other alloying elements may be added at this stage.
3. Casting
Once the steel is melted and refined, it is cast into billets or blooms. These are large, rectangular blocks of steel that will be further processed into the desired shape and size.
4. Hot Rolling
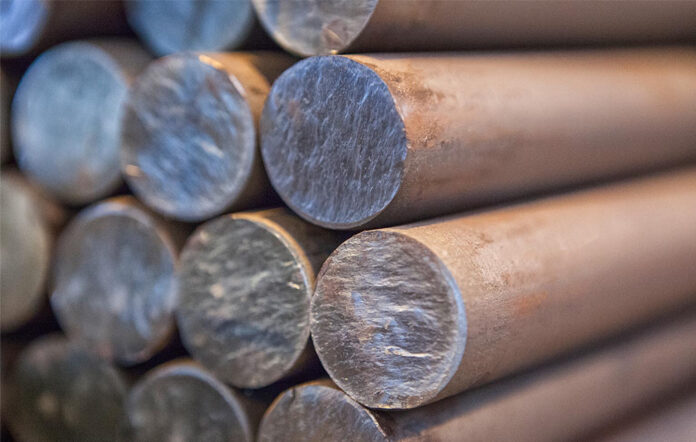
The cast billets or blooms are heated again and passed through a series of rolling mills. This process, known as hot rolling, reduces the thickness of the steel and shapes it into long, narrow strips or coils.
5. Annealing
After hot rolling, the steel strips undergo annealing—a heat treatment process that softens the steel and enhances its ductility. Annealing requires heating the steel to a specific temperature and then slowly cooling it.
6. Cold Rolling
Once annealed, the steel strips are cold-rolled to further reduce their thickness and improve their surface finish. Cold rolling involves passing the steel through a series of rollers at room temperature, which hardens the steel and increases its strength.
7. Tempering
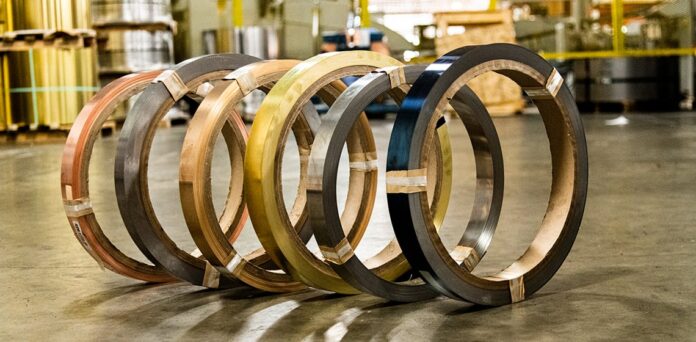
The final heat treatment step in the production of spring steel is tempering. This process involves heating the steel to a moderate temperature and then rapidly cooling it. Tempering increases the toughness of the steel and enhances its ability to withstand stress without breaking. The exact temperature and duration of tempering depend on the specific type of spring steel being produced.
Shaping and Forming Spring Steel
1. Cutting and Forming
Once the steel has been tempered, it is cut into the desired shapes and sizes using various cutting and forming techniques. These techniques include shearing, stamping, and laser cutting, depending on the specific requirements of the final product.
2. Heat Treating and Quenching
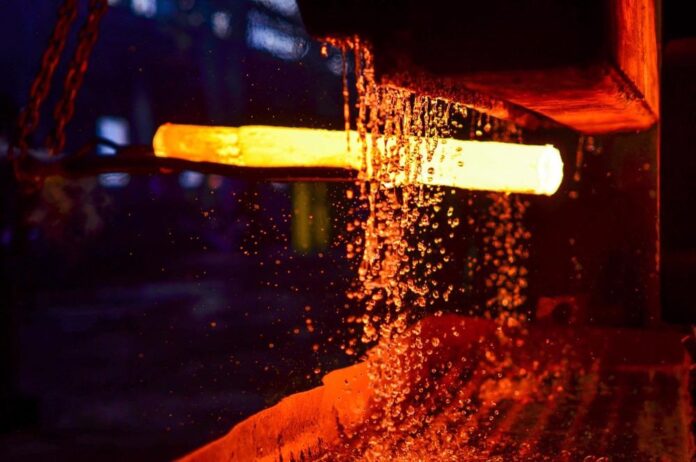
Some spring steel components may undergo additional heat treating and quenching processes to further enhance their mechanical properties. Quenching is the process that rapidly cools the steel in water or oil after heating it to a high temperature.
3. Shot Peening
Shot peening is a surface treatment process used to improve the fatigue strength of spring steel components. It involves bombarding the surface of the steel with small spherical particles, which create compressive stresses and help prevent the initiation and propagation of cracks.
4. Coating and Finishing
The final step in the production of spring steel is coating and finishing. This step requires applying protective coatings, such as zinc or chrome plating, to enhance the corrosion resistance of the steel. The steel components are also polished or otherwise finished to achieve the desired surface quality and appearance.
Conclusion
Throughout the entire production process, strict quality control measures are in place to ensure the spring steel meets the required specifications. This includes regular testing of the chemical composition, mechanical properties, and surface quality of the steel. Any deviations from the standards are corrected to ensure the final product is of the highest quality.