IML stands for in-mold labelling, a common labelling method whereby a pre-printed film is attached to a mold followed by a plastic container. Plastic resin or pellets are then heated and put into the mold, where they blend with the label to develop a final product. Using the right labelling solution is essential, and you must consider several things to make the best decision.
Companies should focus on labels that bring them durability, versatility, and consumer safety. In-mold labels work perfectly with various application forms and produce tremendous graphic reproduction.
Also, in-mold labels are recyclable and regrindable, another significant benefit. This feature is increasingly essential today, considering environmental awareness. In-mold labels are becoming more popular, and we discuss everything you need to know about them.
In-mold labelling was introduced first by Owens Procter and is becoming more popular today and used in various molding companies globally. Product labels are vital to the success of the manufacturers and should be in the best state.
Good quality labels make the product more durable and have an increased lifespan. Research has shown that most people buy goods depending on their emotions, even before considering the benefits they will get.
People’s emotions regarding a particular item are significantly influenced by how they view the product. Beautiful and quality labels attract more clients whose sales impact your company. This explains why most manufacturers pay massive attention to their product’s design and appearance. In-mold labelling is considered among the most effective processes that help organizations get quality product designs.
The In-Mold Labeling Principle
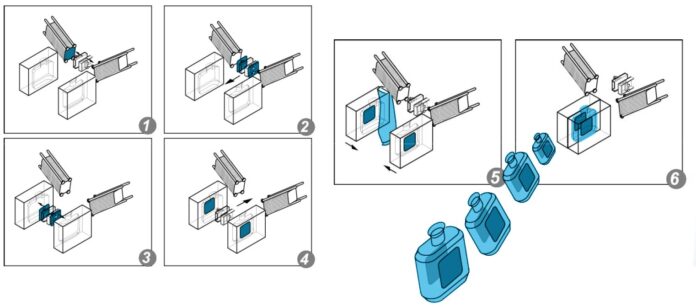
The leading principle of in-mold labelling entails coating products with a design or label layer. This process starts with choosing a unique labelling material. The most commonly used materials include polypropylene, polystyrene, and paper.
The chosen label is put into an open mold and attached to its cavity firmly using a vacuum or clamp, which further creates a beautiful product design.
Benefits of In-Mold Labelling
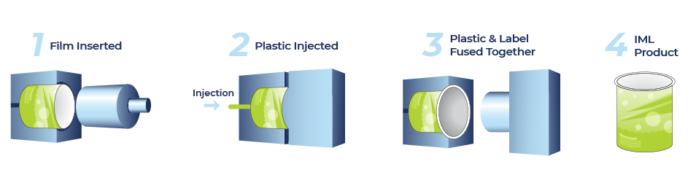
In-mold labelling is versatile and has many benefits to users. The main include;
It Has Different Decorating Options
The main benefit of this labelling is its versatility and ability to provide different decorating options. This process of decorating plastics features quick design changes and maximizes on the use of various colour printing techniques.
Improved Appearance
Another leading benefit of in-mold labels is they improve the product’s appearance. This technique significantly improves your product’s beauty and gives it unique designs. This improved appearance easily draws your customers’ attention, thus increasing sales.
Remember, product information is also shown on the product, which helps companies to improve their brand awareness. This modelling makes a product look more beautiful since it conceals its corners.
The product’s structure also improves since the product and label are developed together; they both touch naturally, thus improving the structure’s appearance. The in-mold label is attached to the product permanently and stays intact throughout its lifespan.
It Enhances Production Efficiency
In-mold labelling has a short production time, and its production is low because manufacturers can produce and decorate containers at the same time. This eliminates the storage cost and makes it unnecessary to store empty containers.
It helps Pinpoint Counterfeit Items
Remember, in-mold labelling demands the use of molds designed uniquely. Manufacturing molds to use in this process requires high-level expertise and capital. However, the high cost and expertise needed for this labelling reduce the occurrence of fraud.
This happens due to the variations in film printing and mold designs, which make it hard for imposters to copy. This feature also helps brands to preserve their dignity.
Which are the Most Common In-Mold Labeling Forming Methods
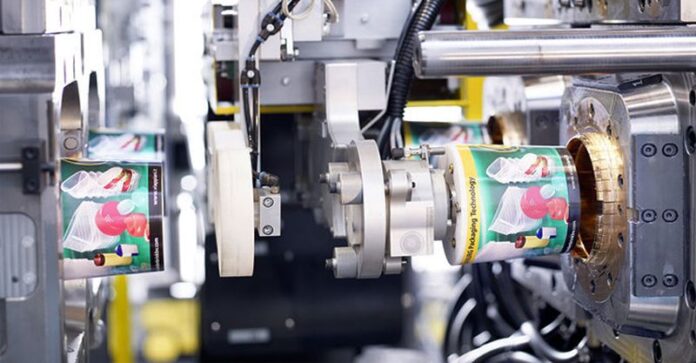
In-labeling can be done in various ways, the primary including;
- Thermoforming
- Blow molding
- Injection molding.
Injection molding
Injection molding is among the most common type of in-mold labelling globally. This process entails heating plastic and cooling it in a mold. The molded part is then fused with a printed label in the mold cavity, which results in a decorated plastic. This process starts with printing a unique label which is put in an open injection using a polymer carrier.
The chosen plastic material is then heated and put in the mold cavity for molding. The injection molding process gives manufacturers excellent design flexibility and is cost-effective. It also offers companies a long-lasting labelling solution that boosts sales.
Most plastic containers use this method, for example, ice cream tubs.
Blow Molding
This is the second most popular mode of in-mold labelling, and it involves stretching heated plastic into a tube. This plastic is then put in a mold, and air is blown into it. As in the above process, a decoration label is placed on the mould’s wall cavity, producing high-quality plastic products.
This procedure is mainly used when manufacturing hollow parts and plastic bottles. The blow molding technique is primarily used to produce liquid containers like those of shampoos or ketchup sauces.
Blow molding is further sub-divided into three categories;
Thermoforming
Here, plastic sheets are heated using a unique tool to form a unique shape. However, the plastic sheets are not heated permanently like in blow molding. The heated plastic is then stretched using a forming tool and forms a mold after cooling.
Thermoforming is mainly used in rigid plastic packaging; it produces plastic cups and tubs used when packing ice cream. Its main applications are;
- Telecommunication
- Storage containers
- Medical devices
- Storage containers.
In-Mold Labeling Markets
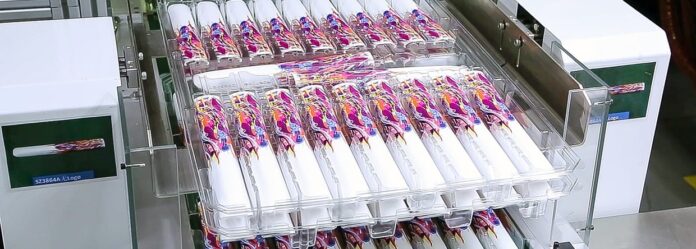
There has been significant growth in in-mold labelling because of its numerous benefits. The in-mold market is expected to witness a considerable increase in the coming years due to the following;
- A significant drop in labelling costs
- These products are recyclable
- This procedure gets rid of all secondary processes in the post-moulding methods.
Most global brands have acknowledged the need to create products with high-quality instructive labels and packaging, and most are using this procedure. This branding enables companies to enhance their brand awareness and provides high-quality labels at affordable rates.
The above article has discussed everything you need to know about in-mold labelling, and you can reach out for more information.