Confused about which electrode to choose? There are several different kinds of welding electrodes available that have different applications. An electrode is a metal wire which is coated and used for welding. The materials used in manufacturing them have the same composition as that of the metal which needs to be welded. When it comes to picking the right fit for your project, numerous factors are to be considered.
Some of these factors include the ease of cleaning up after use, quality of bead, the strength of the weld, and also these should be minimization of any spatter. Additionally, it is critical to store the rods in an environment that is free from moisture, and you should also be careful while removing them from the package.
Welding is a serious job and is also very critical for industries of all kinds. The task is carried out with the help of special machinery that is leveraged to join the bits and pieces of metal together. The process requires a lot of skills and hence, should only be carried out by experienced professionals.
You will find several different kinds of rods that have different applications and are used in different industries. Some of the most common rods and their usage are discussed below.
1. Stick Rod:
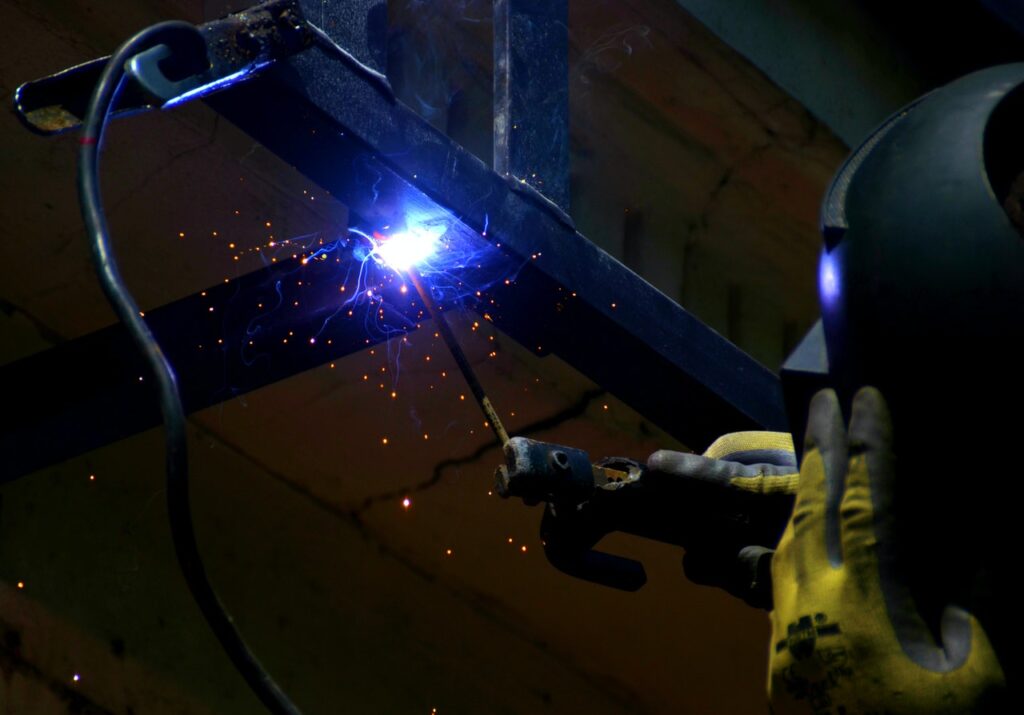
Arc Welding is another name for stick welding. This type of welding electrode was generally used a long time back, but several industries use it today as and when required. It makes use of a stick rod. A very old concept is leveraged to carry out welding using this rod. The stick welding procedure is more complex than the other welding processes, and hence, requires expertise. Anyone who is not trained in the process, cannot guarantee the work done. Looking to buy arc electrodes? Welding.com.au has the best picks.
2. 7018:
This type of welding electrode is generally coated with a very low amount of moisture. It helps in the reduction of hydrogen levels and also deters the rod from seeping deep into the weld too much. Very less amount of hydrogen is present in the electrodes and owing to that the quality of the weld produced is very smooth and powerful. These electrodes are crack-resistant as well.
7018 electrodes are robust and can easily resist a pressure of about 70,000 pounds per cubic square inch. Also, these rods serve numerous purposes. Mould and use it in your preferred way. Iron powder is used to coat this electrode, and it also has a hydrogen coating. Irrespective of whether the current supply is AC or DC, it can operate under both supplies.
These rods must be stored in a moisture-free environment. Also, bear in mind that when exposed to moisture, the lifespan of the electrodes will be impacted.
3. 6013:
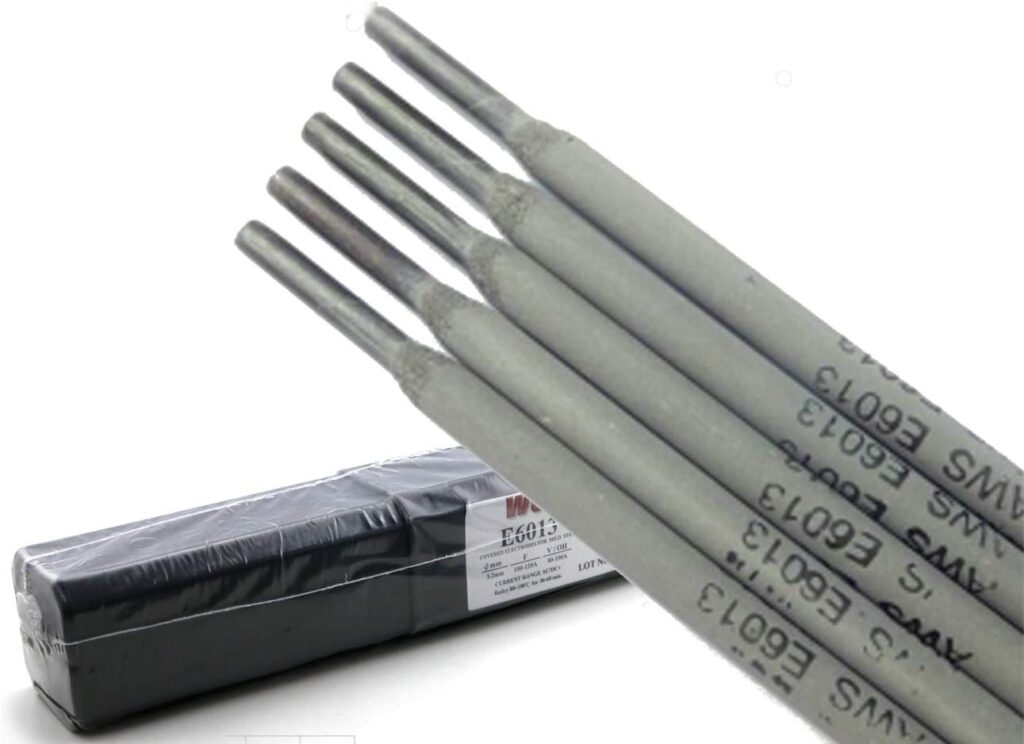
It is one of the most famous types of rods available in the market. It offers the utmost installation convenience and durability. The tensile resilience of this electrode is around 60,000 lbs. Because of its durability, this electrode can be used for several projects. A soft and subtle arc is established at the end that enables the welders to easily mould the sheet of metal. The 6013 welding electrode is also ideal for every small welding job. It is also a great choice when the welders are working with very thin metal sheets, as it allows penetration of medium-range.
This particular electrode can be conveniently used for all different welding positions. Furthermore, it has a high potassium-titanium coating, which makes it an ideal choice to be used for all kinds of currents and power supplies. The rod is highly versatile and can be easily used for welding of all kinds.
The 6013 rods are manufactured using prime steel wire rods. Such rods ensure minimal emission of smoke, low spillage, and also consume a very little amount of electricity. The characteristics of this electrode make it the welder’s best friend.
4. 6011 and 6010:
Both the welding rods are more or less the same and they can easily resist a load of around 60,000 pounds. Both these choices can be effortlessly used for all welding purposes.
The 6011 has a very strong coating of cellulose potassium. It also indicates that both the choices can be easily used with both AC and DC types. The electrodes can also be used in welding machines of a much bigger size. The 6011 type is the best pick for deeper penetration welding. It is also suitable to be used with corroded and dirty metals. Both the choices are ideal for all kinds of repair jobs.
On the contrary, the 6011 electrode has a strong coating of high cellulose sodium. It depicts that the electrode is used only with DC current. This type of electrode can also attain deeper penetration and works best with metals that are corroded or dirty.
5. 6012:
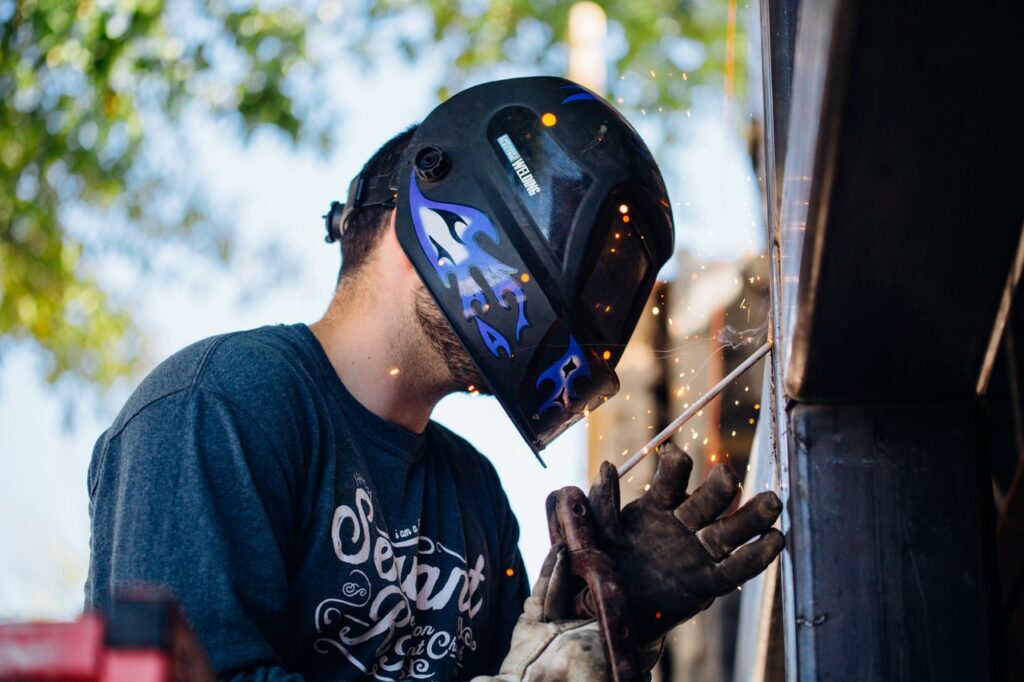
This is a general-purpose rod that has a great bridging characteristic and is particularly applied with sub-par-fit-up. This kind of rod is known for providing an adequate amount of stable arc, and can feasibly run on super high currents with minimal spatter. This electrode is also friendly with both the AC and DC types.
One of the major limitations of using this electrode is that it is suitable only for thin and shallow penetration. Another limitation is that when smelted it generates a very thick waste material. That beinf said, when used it requires an additional clean-up after the welding procedure is complete.
The typical applications of this type of electrode include connecting some kind of open joints, non-critical welding, repair works, and is also used for the welding of carbon sheets that are rusted.
Summary
Welding is a tedious task, and it is required that you choose a rod that is most suited for your project to get away from all kinds of worries. Several different kinds of welding rods are available in the market nowadays, and you can easily pick one as per your needs and requirements.